Fabric first double storey self-build
It was by complete luck that Daryl Cann fell into his own self-build journey.
He stumbled across a plot, a five-minute walk from his mum’s house in September 2018. It was a red brick ex-council house reduced in price. He immediately spotted its potential.
He recalls: “The plot was massive, and it had been reduced from £195,000 to £185,000. From the moment we were shown around the house I thought it had so much potential, I looked past the outdated room layouts and overgrown garden to envisage a beautiful family home.”
His head racing with ideas, Daryl consulted his wife Gemma and within days their house was on the market, and it sold four days later.
With £65,000 equity from the old house, Daryl believed he could make a “huge dent” in the cost of remodelling the red brick into a modern double-storey property. The couple placed an offer for the generous plot, complete with a three-bedroom, semi-detached house.
Offer accepted, and the race was on to reconstruct the existing build with a double storey extension to the side and a single storey to the rear. With the help of colleague and part-time architect, Jon Mead, the couple envisaged a new en suite master bedroom, two double bedrooms, a family bathroom on the first floor and generous open plan living on the ground floor.
Architectural harmony was key, with Daryl choosing a mixture of render and horizontal timber cladding to uplift the tired nature of the existing dwelling and decorated in a colour to blend in architecturally. Windows and doors were specified to bring a refreshing appearance to the property. The whole roof was replaced and natural slate effect tiles created a more modern, clean look.
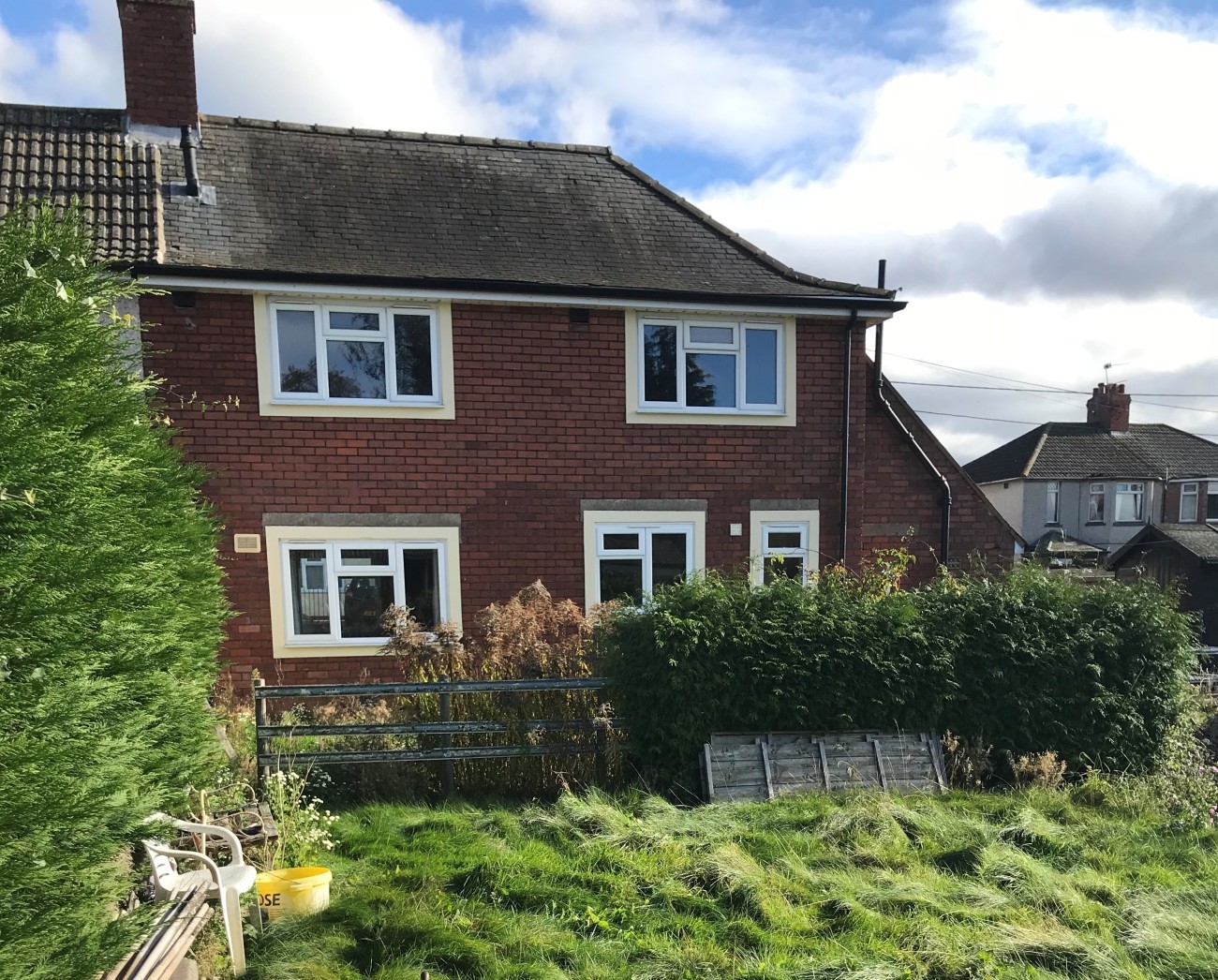
With a head for figures and knowledge of the insulation market, Daryl, who works in commercial sales, knew a fabric first approach was the only way he could transform the draughty, red brick house into a warm, comfortable living space.
“The old house was a modest 1920s red brick house with poor insulation and damp. We wanted to put our stamp on the place, but it soon became apparent that this wasn’t a do-er upper. We had to start again by demolishing the existing build and re-building around its carcass.”
The couple and their toddler Archie moved into Gemma’s parents’ house at the end of 2018, allowing the family to live rent-free. Daryl, also in full-time employment, began working around the clock, with the aim of completing the build within a year.
“Although the existing building had foundations and services connected, we decided to dig up all of the existing internal foundations and start again, as well as move all of the connecting service entry points into the house. In hindsight, it would have been easier if this was a “traditional” self-build where you start with a plot of land from scratch.
“Ultimately we had to apply for planning permission for the double storey extension to the side and single storey extension off the back. We only required planning permission for the proposed extension and alterations rather than a replacement dwelling.
“I did the majority of the work myself with help from friends, family and specialist contractors. I made a huge dent over the summer in the evenings and weekends, but it was a real juggle.”
Once planning permission was submitted in November 2018, a month later they received the go-ahead and keys for the house in January 2019. Demolition could finally get underway, a task Daryl relished.
Their architect, Jon, was employed to bring their vision to paper and specialist contractors included a bricklayer, timber framer, electrician, plumber, and plasterer. As for the rest – demolishing, foundations, subfloors, insulating, plaster boarding, landscaping, decking, decorating, and project managing came under Daryl’s remit.
He says: “We didn’t have a huge budget and there were specialist skills I didn’t have so it was important to enlist the help of professionals. The fabric of the build was really important to us as we knew this will affect the energy efficiency and warmth of the build in the long-term.
“We were lucky that planning permission was a swift process, and our neighbours were happy with our plans. We live in a small village and all the houses are wildly different so that was in our favour.”
The extension is constructed around a timber frame with 120mm insulation between the timber studs. Celotex PIR Rigid Insulation sheets were installed in the external walls, followed by a 12mm sheet used internally to stop thermal bridging, part of the fabric first approach. Other materials used include 200mm Celotex in the pitch of the new roof, and 50mm added to the internal wall of the existing red brick walls. With all of this insulation the house holds the heat for longer ensuring a warm comfortable living space, explains Daryl.
“Using materials like British Gypsum DB Sound Board and Isover Acoustic Partition Roll (APR 1200) ensures sound transfer is kept to a minimum between the bedrooms – helping my family to sleep better."
"We didn’t skimp on the fabric of the build, but we wanted a fast and efficient build, which is why we chose a timber frame as I knew it would be a swifter process. We removed all of the existing beams on the first floor and at one point the house resembled a church!
Products like British Gypsum Multi Finish Plaster and British Gypsum Bonding Coat were used by my plasterer as I knew the quality of brand and would except nothing less than perfect on my finished walls.”
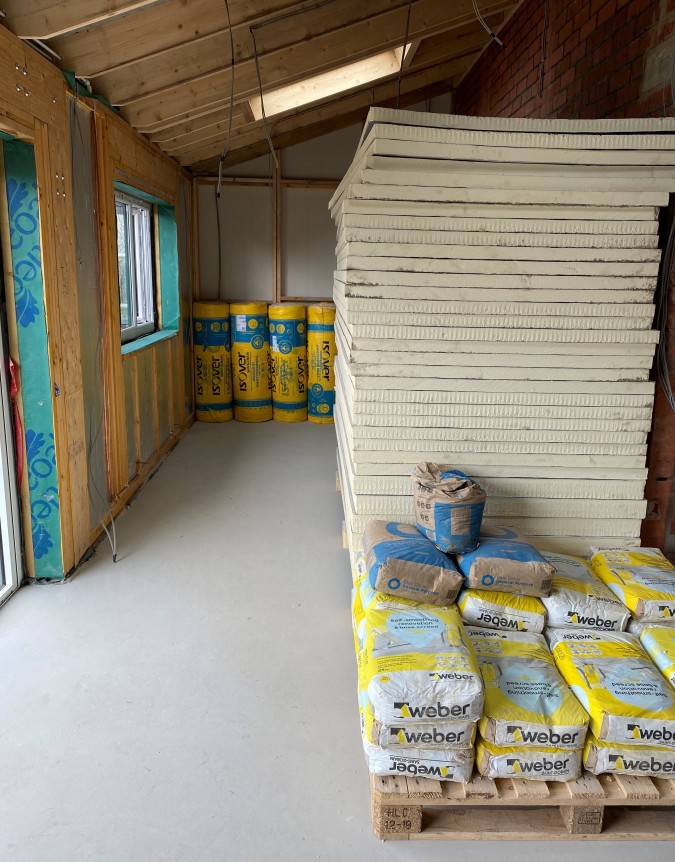
Lockdown brings light
The global pandemic hit in March 2020 and Daryl was furloughed. This became his golden opportunity to push on with the build.
He said: “It was a worrying time being put on furlough and with financial uncertainty in the air I didn’t have any choice but to plough on with the project. Throughout lockdown I made the most of the “extra time” and made a nice dent in project progress. I worked this out to have effectively saved me six months of weekend work.
“A huge highlight was when the new roof was finished, the windows and doors installed and the house became watertight. My father-in-law fits windows and doors for a living so he was able to get these sorted at a heavily reduced price.”
In January 2021, the family moved into their new modern three-bedroom house. The open plan layout links the entrance, kitchen, Velux room and stairway ensuring plenty of natural light floods the heart of the house – a key factor to improving wellbeing and mood, says Daryl.
“My favourite features of the house have to be the built-in fireplace feature wall, the open landing at the top of the stairs and the 3.6m bi-fold doors, which help to bring the outside in – when you walk through the front door your eyes are drawn to them and you see straight out into the garden. I also love our attic, with futureproofing in mind, we paid extra for attic trusses rather than the standard W design which allows us to utilise the space in the attic.”
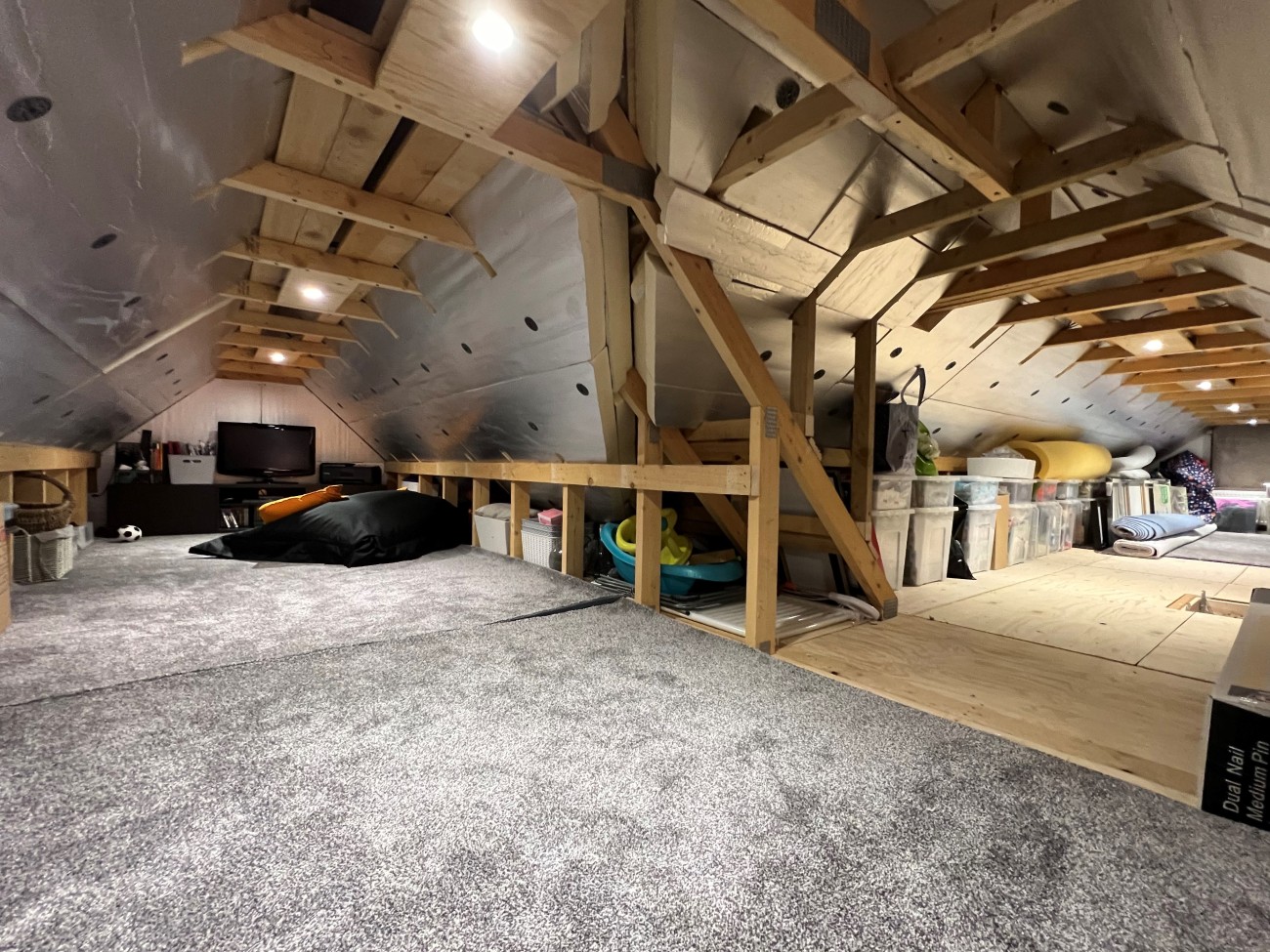
Money talks
When it came to budgets Daryl took a more relaxed approach.
He explains: “It might sound weird, but I didn’t really work to a designated budget. As my wife, son and I were lucky enough to live at my in-laws rent free during the build, we were able to spend that money on what was required on the project at that time.
“We started with £65,000 from equity in our old house, then required personal loans to see us over the line. We did pay attention to cost savings, for example we managed to re-sell the red imperial bricks from the old property which we dismantled and cleaned – earning almost £2,000.
“As I didn’t work to a budget not a lot of it could change, it meant some elements were delayed as I had to use the money elsewhere first. I tried to plan where money was needed next logically rather than assign every part of the build a specific amount of money. Things that I hadn’t planned on spending so much on were things like Catnic lintels over doorways and windows, radiators and LED strip lights in the kitchen – just these three things came to more than £4,500.”
The ups…and the downs
“There have been so many highs and lows in this build. From the day the scaffolding came down to reveal a newly rendered house to getting electricity inside which meant I didn’t have to run an extension lead from the outside mains box through the mud, and up through a window!
“As for lows, it had to be the day I took down my old roof with a reciprocating saw and a step ladder. All that remained was a front wall and back wall braced together with an installed steel frame to ensure the walls didn’t fall over (like an open cardboard box). This was a tough day. Funnily enough that was when my wife stopped coming round to see how things were progressing for a while!”
“This is our forever home. Yes, it took huge sacrifices and a lot of time. But my family and I now live in a house that I wouldn’t have been able to buy – this makes all the hard work worthwhile. The day we moved in was so memorable, just seeing my wife and son’s reaction made it feel like home instantly – everything was for this moment!”
It was a worrying time being put on furlough and with financial uncertainty in the air
Advice for self-builders:
1/ One of the biggest expenses of a self-build is labour. If you are reasonably handy then do some research, watch some YouTube videos and give it a go. Even doing small things like moving bricks and blocks to where a bricklayer will need them goes a long way.
2/ Project manage your self-build by using project management tools like a dependency matrix or Gantt chart. These will highlight what tasks are dependent on others – this way you can clearly see what tasks need to be completed before another is started.
3/ Be resilient – at times, your to-do list will seem overwhelming. Chip away at tasks one at a time and visualise how good it’s going to look once completed, not how much you’ve got left to do.
4/ Keep the site as tidy as possible as there is nothing worse than turning up to site at 6am on a dark and dreary day. The last thing you want is to walk into a messy site – this is not good for morale.
5/ Once a month (for me, it was the last Sunday of the month) take a day off to spend with family or friends. Don’t do anything to the build, just spend some quality time with the ones that are supporting you throughout the project – this is very important.
What is a fabric first approach?
The fabric first approach allows for simple changes considering the design, construction and building fabric of a home to produce an efficient and low energy building.
The building fabric refers to the roof, walls, windows, floors, and doors of a building. And within these elements, you can make smart choices as to which materials you use, to make sure your building needs as little energy as possible to keep it warm and comfortable all year round. Whether that’s choosing the right level and performance of insulation in your walls, floor and roof, how you reduce draughts, or the performance of the windows you choose.
What are the benefits of applying a fabric first approach?
- Reduced energy costs
- Improved temperature control
- Comfortable all year round
- Lower running costs
- Reduced chance of condensation or mould (don’t forget to manage ventilation well)
Saint-Gobain products used:
- Isover Acoustic Partition Roll (APR)
- British Gypsum Plasterboard
- British Gypsum Multi Finish Plaster
- Celotex PIR Insulation
- International Timber
- Weber Mesh
- Weber Rend Aid
- Weber Render
- Weber Screed
Products like membranes, sand, cement, ballast, MOT Type 1, bricks, blocks, OSB Board, plywood sheets and screws – all from Jewson.
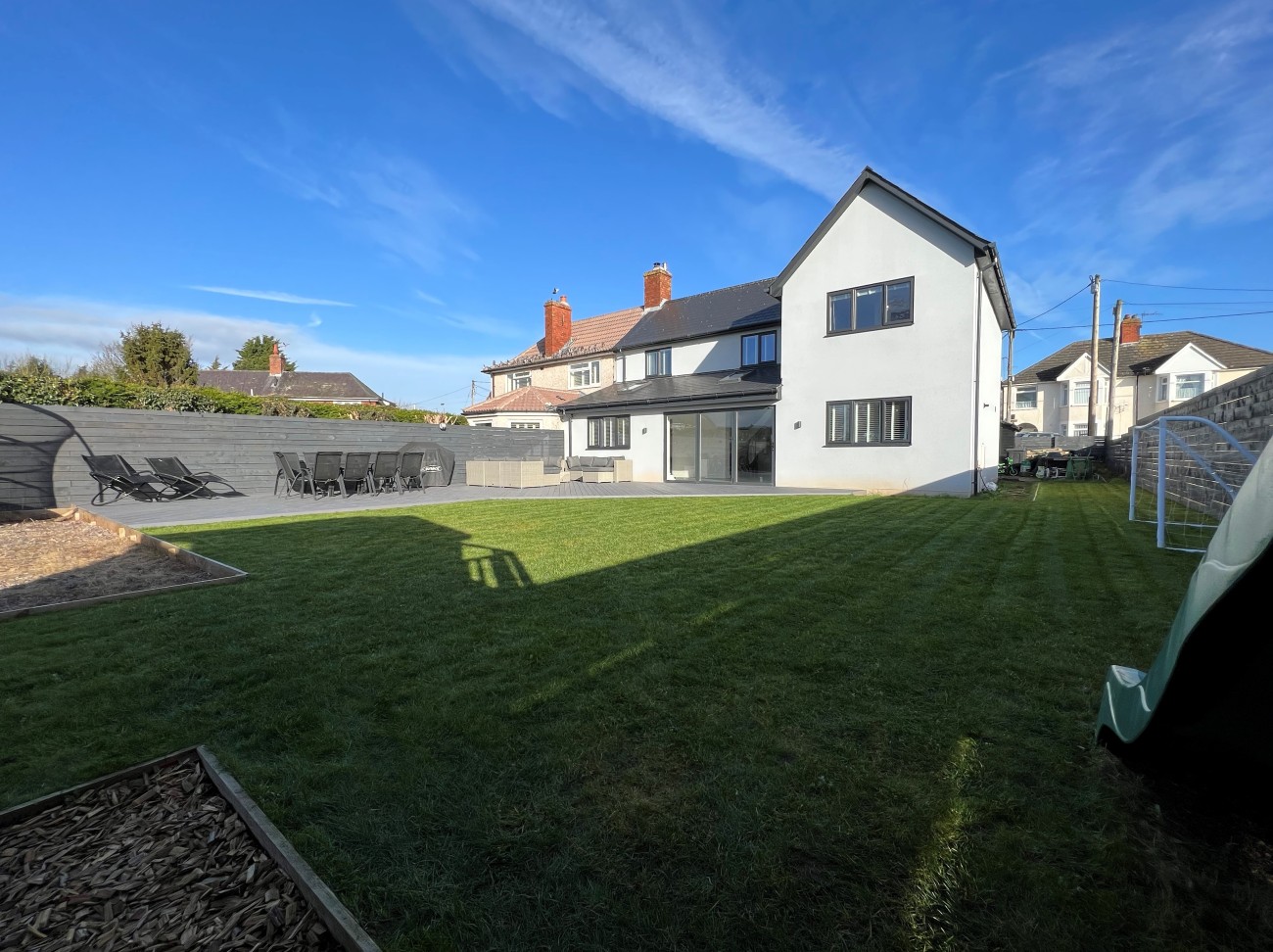