Confessions of a Self-Builder: Part 5
We're following James Mason on his second self-build journey, you can follow from the very start with his previous blog posts, or read on to find out where he's got to this month.
Taking on the role of self-build project manager is a huge task. In my first self-build I was faced with so many challenges but after it was done and dusted it was easy to forget all of those intricacies and niggling issues.
But my current project has definitely tested me.
Who knew that I’d be working 18-hour days to get our home finished. Since the coronavirus crisis hit us globally, I’ve been desperately trying to keep my timber frame self-build project on time and on budget. But it’s been impossible.
Three lockdowns later and we’re still living in our rental home which is costing us almost £800 a month – we’re already looking at almost £10,000 in rental costs which I hadn’t planned for. The original plan was to move into our home in August 2020 but we’re way behind schedule and we’re hoping to move in by May or June this year.
The race to the finish line is now on and when I finish my work shifts at 7am it’s straight to the site to check progress and get things moving along.
Discover James' first self-build home in our case study: The Contemporary Home.
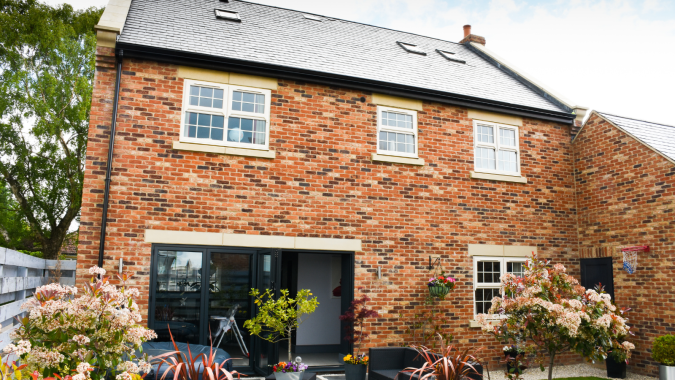
Weather woes
The weather has been truly horrendous and possibly one of the worst winters we’ve seen in years. The rain and floods over Christmas meant water poured in and the snow in North Yorkshire caused delays to our roof but the tiles are finally on and it’s almost complete. We chose blue Spanish slate – it’s not a cheap material. Each tile has to be nailed to the roof but we’re pleased with the result and glad we chose a grade A quality tile.
My wife Rachael has been busily scraping away to ensure all of the floors are level so we can lay the floor screed. We’re using a local company which is supplying a fast-setting liquid screed along with all the heating materials, piping, manifold and stat controls.
The need for screed…and speed
We had the option of sand cement floor or liquid floor screed. We chose the latter as sand and cement takes 1mm a day to dry out and our floor depth covering is 75mm so would have taken 75 days to dry. We simply couldn’t wait that long! Liquid screed costs more than other types of screeds but it’s worth it for the speed in which we can work, cutting down time and allowing us to push ahead with laying plasterboard and flooring.
Elsewhere, there have been some changes to the floor layout around the entrance hall and upstairs we decided one of the en-suite bathrooms was a bit cramped so we expanded the space.
Is it a great idea to make changes at this stage? Not really, but it’s worth doing it now rather than regretting it later on. Now we’ve finalised these changes I can crack on with ordering sanitary ware.
It’s brilliant to see the first fix complete – a watertight self-build ready for the next stages. Once the flooring is down then it’s onto the internal plastering. We are using 15mm Gyproc Wallboard and 12.5 British Gypsum SoundBloc on the ceilings as we have noisy children!
One thing to remember with timber frame construction is to make sure you put your patches in for anything you may need to hang from the wall before you install the plasterboard (for example radiators and TVs). I have used 4x2 inch nogs for the radiators and 11mm OSB boards for TV brackets.
Another thing to bear in mind is that you really don’t want cables to run down stonework so when it comes to installing TV aerials and Sky, call your companies to obtain the cables before you install plasterboard.
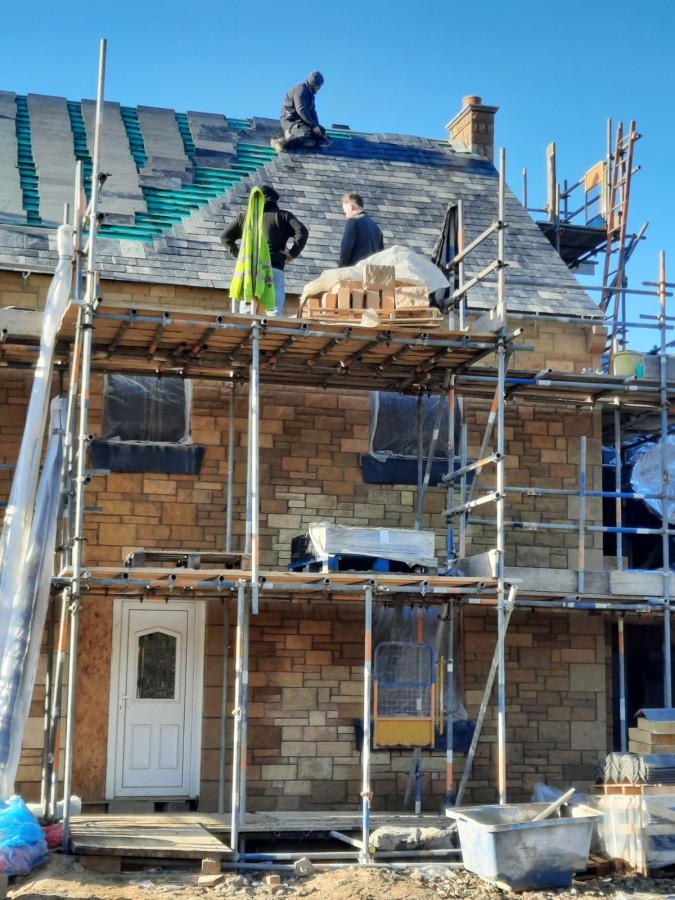
Taking shape
Although it’s super busy, it’s lovely to see our house taking shape and with three different elevation changes across the property you can see how amazing it looks – particularly at the rear of the build.
The Velux windows are in and looking up at the vaulted ceilings in the kitchen is a joy. We may not have all of our lighting but I am currently sourcing some recess lights, which are proving to be costly but just one of those things you find yourself needing!
Sourcing supplies and navigating through so many unknowns has been tough but with the support of my wife Rachael I know we can get through it all. She is fully behind our timber frame self-build project, as are all of my friends and colleagues who have offered a pair of hands to get us to the finish line.
I am so glad that we’ve had a brilliant architect who I’ve been able to ring up for advice and support. Yes, it’s been a tough year but I definitely feel more confident than my first self-build and I know whatever needs doing, we’ll sort it! In the meantime, I’m dreaming of the day I can relax in my snooker room on the top floor and seeing all the family at home…that’s what keeps me going!