Your guide to timber frame houses
Why timber frame?
Timber frame construction is continuously growing in popularity across the UK, and remains an ever popular choice in Scotland and Scandinavia where the wet climate restricts build time. In fact, the timber frame construction market report (UK) 2018 by MTW Research forecasts a 25% growth in the timber frame construction market by 2022.
And timber frame buildings are a very popular choice with self-builders. This kind of frame provides a wide range of design options - from a traditional brick-faced look to the wooden Scandinavian finish. The longevity of this build method is indicated through the timber frame homes that have stood for centuries. Given appropriate treatment and ventilation, modern timber-framing is extremely resistant to rot, fire and insect attack.
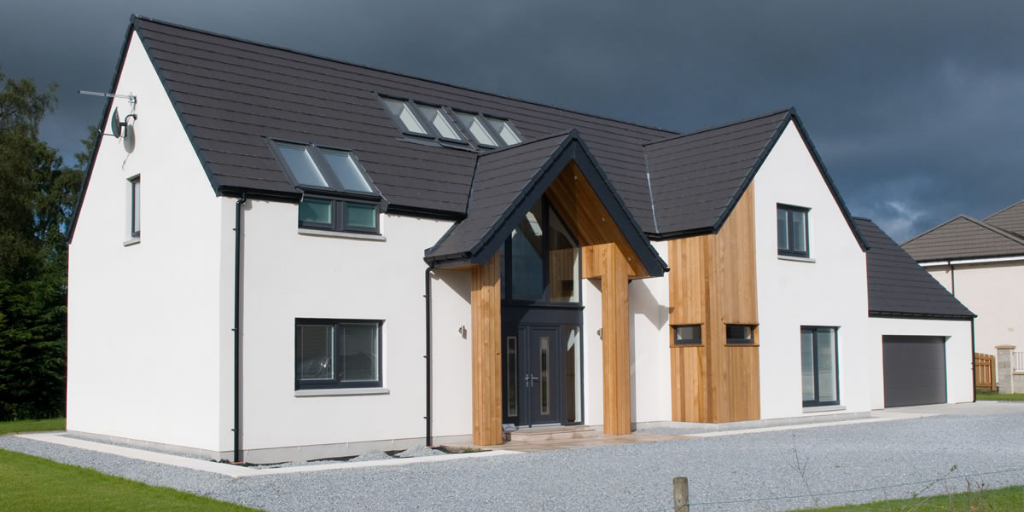
Types of timber construction
There are three main types of wood construction. These include timber frame which is precision engineered, strong and durable. The build method relies on timber frame as the basic means of structural support, utilising factory manufactured wall, floor and roof panels.
Structural Insulated Panels (SIPS) are an advanced method of construction, offering structural strength and airtightness. SIP technology has been developed around composite panels and is used in floors, walls and roofs.
Cross-laminated timber (CLT) is a solid panel product, formed from softwood plank layers laid on top of each other at right angles, glued together under pressure. CLT is used more on residential projects.
Benefits of timber frame
Offsite manufactured structural timber systems have grown in popularity as they can be built faster and have better thermal efficiency, which can reduce the running costs of a building. The lightweight nature of timber frame systems means they are suitable on brownfield sites with poor soil conditions.
Structural timber can deliver a number of advantages, in both the long and short term – it’s sustainable, economic, thermally efficient and can be constructed quickly.
Quick construction
Timber frames require less time to dry out ahead of internal work such as decorating and electrical installation. This can commence as soon as a timber frame is weatherproofed. Low temperatures are no hindrance and if poor weather is likely, timber-frame construction will quickly enclose areas requiring further work, which would be considerably delayed within a masonry frame. Your home can be erected and watertight in around five days and factory prefabrication makes for simple on-site assembly.
Because it is a dry construction, a new home can be wallpapered immediately without any fear of staining or cracking and there is no drying out period. Wallpapering, carpeting and tiling are made easier by the accuracy of timber frame.
Energy efficient
Timber frame homes are engineered to be draught-free and generously insulated so that the energy needed to run your home is significantly reduced. Most modern masonry homes have external walls made of concrete blockwork on the inside and brick on the outside, with thermal insulation in the cavity between.
Cost is everything when it comes to your self-build project and timber can allow for more accurate budgeting. Timber has superior thermal efficiency, which means that the building remains warmer in the winter and cool in the summer – reducing your energy bills.
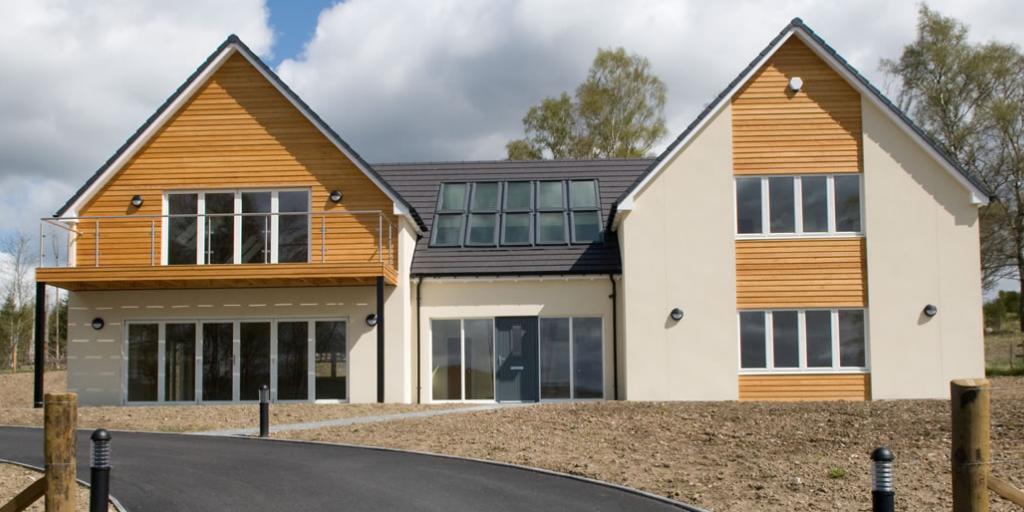
Open or closed panels?
Scotframe provides timber kit packages to self-builders and contractors in the UK, which come in open panel timber frames or closed panels.
Open panel timber frames are manufactured with the internal side of the walling element unsheathed. Closed panels insulation is pre-fitted and in some cases the doors, windows and plasterboard are already in place.
Sales Director Malcolm Thomson says that a lot of builders do opt for a closed system, which are faster to erect and can achieve excellent airtightness levels.
“Timber frame systems are popular in Scotland with 83% of new builds using this material. The trend is rising in the UK. When it comes to cost – on average you’re looking at between £1,300-£1,600 per square metre, for a complete build package (including foundations) dependant on specification, ground conditions and utilities connections.
“The timber we use is mainly CLS (Canadian Lumber Standard) and is mainly sourced from Scandinavia and from Canada.”
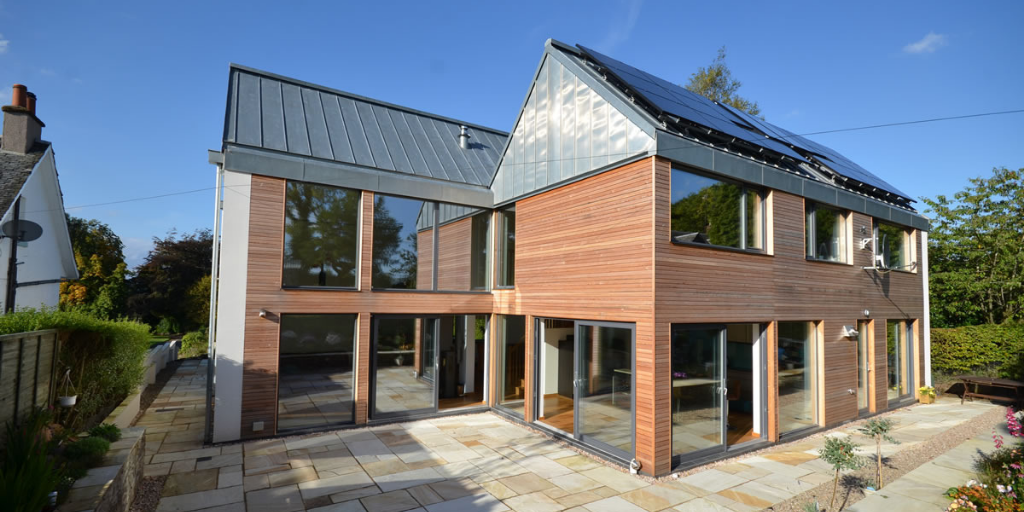
Timeframes
Bear in mind that the precise design for a timber frame must be finalised in advance of manufacture, and allowance of factory-time (8 – 12 weeks dependant on complexity and time of year) needs to be included in your schedule. On average you’re looking at between four to six months in total for construction - but it all depends on your project and planning permission.
A real timber home
Aberdeenshire couple Lee and Iain Jaffrey purchased their timber frame home from Scotframe. The couple and their young family moved into Denwell Cottage on the outskirts of the village of Insch, 28 miles north west of Aberdeen, and are reaping the rewards of a spacious, open-plan home with minimal energy bills.
Denwell Cottage was designed by Annie Kenyon Architects and constructed for the Jaffrey’s by Gregor and Kate Davidson of Ellon-based Cairnrowan Custom Homes, who brought the project from kit arrival to achieving entry in just 14 weeks.
The walls and roof cassettes of Denwell Cottage kit use Scotframe’s Val-U-Therm PLUS panels, which have proven their value in maximising airtightness, use of insulation and the thermal performance of the building fabric. The cottage was named a finalist for Best Timber Home in the Build It awards 2018.
Read the Denwell Cottage case study here.